The Most Advanced, Modern 3D Printer Creations
Introduction
3D printing or additive manufacturing is a process of making three dimensional solid objects from a digital file. The creation of a 3D printed object is achieved using additive processes. In an additive process an object is created by laying down successive layers of material until the entire object is created. Each of these layers can be seen as a thinly sliced horizontal cross-section of the eventual object.

A MakerBot 3d Printer | “MakerBot ThingOMatic Bre Pettis” by Bre Pettis – Flickr, specific image page URL: http://www.flickr.com/photos/bre/3458247336/. Licensed under CC BY 2.0 via Commons.
3D printing is performed by machines called 3D printers. They are classified as industrial robots because of their self-moveable arm that cuts or builds designs into the substrate. (An industrial robot is defined by ISO 8373 as an automatically controlled, reprogrammable, multipurpose manipulator programmable in three or more axes.)
3D printing dates back to 1980s. It was invented in 1984 by Chuck Hull. He developed a prototype system based on this process known as stereolithography, in which layers are added by curing photopolymers with ultraviolet light lasers. Hull defined the process as a “system for generating three-dimensional objects by creating a cross-sectional pattern of the object to be formed. This technology used by most 3D printers to date – especially hobbyist and consumer-oriented models.
Since the start of the twenty-first century there has been a large growth in the sales of 3D printing machines, and their price dropped substantially. The technology is used in the fields of jewellery, footwear, industrial design, architecture, engineering and construction (AEC), automotive, aerospace, dental and medical industries, education, geographic information systems, civil engineering, and many others. For example, General Electric uses 3D printers to build parts for turbines.
How does it work?
The process of 3D printing can be described in the following three systematic steps.
1. Modeling
3D models are first created with a computer aided design (CAD) package. Alternatively they can be created with a 3D scanner, a digital camera and photogrammetry software.
The manual modeling process of preparing geometric data for 3D computer graphics is similar to sculpting. 3D scanning is a process of analysing and collecting data on the shape and appearance of a real object. Based on this data, three-dimensional models of the scanned object can then be produced.
Regardless of the 3D modeling software used, the 3D model (often in .skp, .dae, .3ds or some other format) then needs to be converted to either a .STL or a .OBJ format, to allow the printing (a.k.a. “CAM”) software to be able to read it.
2. Printing
Before printing a 3D model from an STL file, it must first be examined for “manifold errors,” this step being called the “fixup.” Especially STLs that have been produced from a model obtained through 3D scanning often have many manifold errors in them that need to be fixed. Examples of manifold errors are surfaces that do not connect, or gaps in the models.
Once that’s done, the .STL file needs to be processed by a piece of software called a “slicer” which converts the model into a series of thin layers and produces a G-code file containing instructions tailored to a specific type of 3D printer (FDM printers). This G-code file can then be printed with 3D printing client software (which loads the G-code, and uses it to instruct the 3D printer during the 3D printing process).
Construction of a model with contemporary methods can take anywhere from several hours to several days, depending on the method used and the size and complexity of the model. Additive systems can typically reduce this time to a few hours, although it varies widely depending on the type of machine used and the size and number of models being produced simultaneously.
Traditional techniques like injection moulding can be less expensive for manufacturing polymer products in high quantities, but additive manufacturing can be faster, more flexible and less expensive when producing relatively small quantities of parts. 3D printers give designers and concept development teams the ability to produce parts and concept models using a desktop size printer.
3. Finishing
Though the printer-produced resolution is sufficient for many applications, printing a slightly oversized version of the desired object in standard resolution and then removing material with a higher-resolution subtractive process can achieve greater precision.
Some printable polymers allow the surface finish to be smoothed and improved using chemical vapour processes.
Some additive manufacturing techniques are capable of using multiple materials in the course of constructing parts. These techniques are able to print in multiple colors and color combinations simultaneously, and would not necessarily require painting.
Some printing techniques require internal supports to be built for overhanging features during construction. These supports must be mechanically removed or dissolved upon completion of the print.
Some wonderful 3D printing creations
3D printed acoustic guitar
Scott Summi created the world’s first 3D printed acoustic guitar. With 3D printing, guitars can be made with plastic, complete with the metal soundhole cover and heel joint. Apart from making working musical instruments, avid guitarists can also make a 3D replica of the guitars of their favorite musicians or idols.
3D fetus
“3D scans” of your unborn child is taking on a whole new meaning. Instead of a picture of your ultrasound, a Japanese company is now giving you a ‘Shape of an Angel’, a 3D print of your foetus for $1275. The 3D model is created by 3D processed image data with BioTexture.
Shakuhachi Flute
This is a beautiful Japanese flute made out of stainless steel, 3D printed. It comes with a few different finishes such as gold plated matte or glossy and antique bronze matte (pictured below). The flute is 9.4 inches long and has a tiny dragon design if you look closely enough.
3D Printed Medical Models
When it comes to tech, science has to have a dab in it. With 3D printing, doctors would have a cheaper alternative to learn about the human anatomy and also be able to inject realism into surgery practice without the use of cadavers.
Since the printing of these medical models is so accurate, surgeons can also plan a surgery on a printed model like this before the real patient goes under the knife.
Electric light shoe
This shoe filled with intricate detail and lights is 1 meter long and not a pair of shoes you can wear. It was used as an Onitsuka Tiger commercial and created with a 3D printer. The link says you can purchase it for 5879.83 Euros and keep it as a modern sculpture in your home.
Gear wraps
If you like to bring your gear around with you and want it to be organized neatly, then you could buy this 3D printed Gear Wraps that can save you the hassle and time of untangling your many cables.
It can be printed in a wide variety of different colors and ranges from a price of 10 to 20 Euros depending on the color you choose.
Infinite Sisu – iPad Stand
This stand is inspired by a Finnish concept of determination; the little muscular ‘man’ holding up the iPad is pretty hard to miss. This is definitely a work of art which you can purchase at a price of $161.
It might seem pricey for an over-glorified smartphone or tablet stand, but it’s the hefty price you pay for any kind of beautiful art.
Hanging Light
Janne Kyttanen created this eye-catching work of art which comes in a variety of sizes. Use it as part of your decor, as a standing lamp, a table or ceiling light fixture.
Kaleidoscope Clock
Here is a two-piece 3D-printed clock, which comes in two parts, Part A and Part B. The clock is split into 2 ‘faces’, the purple numbered face and the design face behind it.
With a few instructions, you can put the two together and have it up and running in no time. The white Kaleidoscope Clock kit is available for a total of $51 or a black one for $61.
3D Anatomica di Revolutis Sculptural
This work of art is the creation of one of the most recognized 3D printing designer Joshua Harker. It’s printed with polyamide, a combination of nylon and glass fused together with a laser. Check the link out for more close-up photos of this fascinating and intricate creation.
3D printing methodologies
Some of the significant 3D printing methods are briefly described below.
Electron beam melting
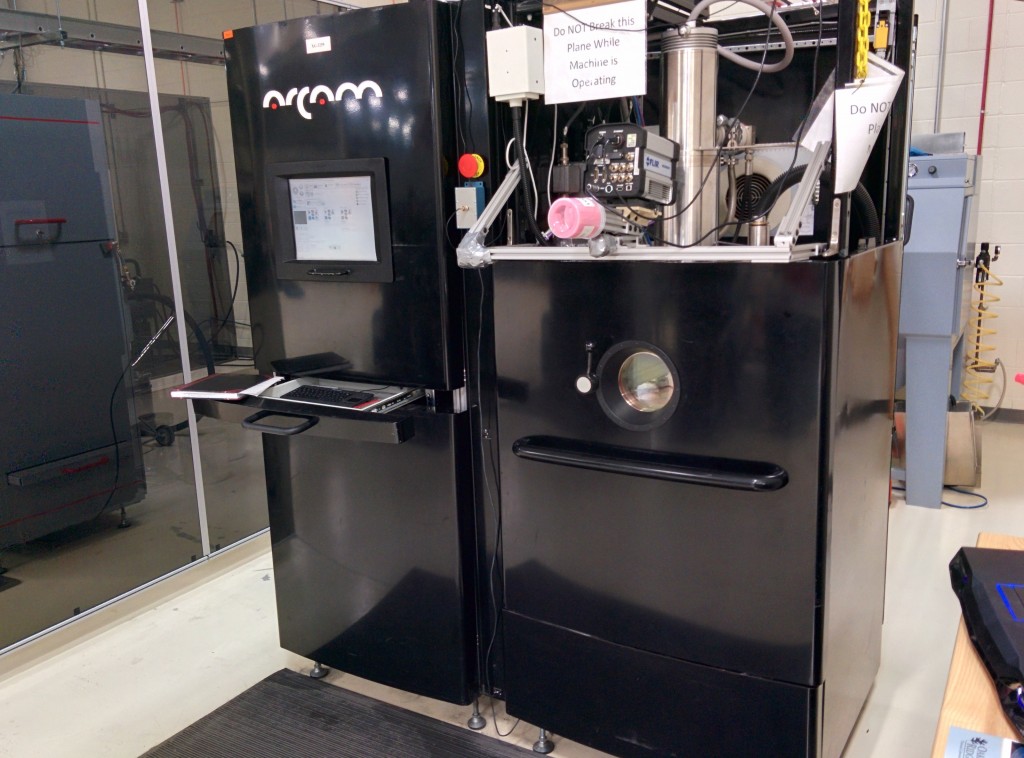
Arkam A2 electronic beam melting machine | “Arcam A2” by William Sames – Own work. Licensed under CC BY-SA 4.0 via Commons.
EBM uses an electron beam as its power source, as opposed to a laser. EBM technology manufactures parts by melting metal powder layer by layer with an electron beam in a high vacuum. This solid freeform fabrication method produces fully dense metal parts directly from metal powder with characteristics of the target material. The EBM machine reads data from a 3D CAD model and lays down successive layers of powdered material. These layers are melted together utilizing a computer controlled electron beam. In this way it builds up the parts. The process takes place under vacuum, which makes it suited to manufacture parts in reactive materials with a high affinity for oxygen, e.g. titanium.
Stereolithography
Stereolithography is an additive manufacturing process which employs a vat of liquid ultraviolet curable photopolymer “resin” and an ultraviolet laser to build parts’ layers one at a time. For each layer, the laser beam traces a cross-section of the part pattern on the surface of the liquid resin. Exposure to the ultraviolet laser light cures and solidifies the pattern traced on the resin and joins it to the layer below.
After the pattern has been traced, the SLA’s elevator platform descends by a distance equal to the thickness of a single layer, typically 0.05 mm to 0.15 mm (0.002 in to 0.006 in). Then, a resin-filled blade sweeps across the cross section of the part, re-coating it with fresh material. On this new liquid surface, the subsequent layer pattern is traced, joining the previous layer. A complete 3-D part is formed by this process. After being built, parts are immersed in a chemical bath in order to be cleaned of excess resin and are subsequently cured in an ultraviolet oven.
Selective Laser Melting
Selective laser melting is an additive manufacturing process that uses 3D CAD data as a digital information source and energy in the form of a high-power laser beam, to create three-dimensional metal parts by fusing fine metal powders together.
The process starts by slicing the 3D CAD file data into layers, usually from 20 to 100 micrometres thick, creating a 2D image of each layer; this file format is the industry standard .stl file used on most layer-based 3D printing or stereolithography technologies. This file is then loaded into a file preparation software package that assigns parameters, values and physical supports that allow the file to be interpreted and built by different types of additive manufacturing machines.
With selective laser melting, selectively melts thin layers of atomized fine metal powder are evenly distributed using a coating mechanism onto a substrate plate, usually metal, that is fastened to an indexing table that moves in the vertical (Z) axis. This takes place inside a chamber containing a tightly controlled atmosphere of inert gas, either argon or nitrogen at oxygen levels below 500 parts per million. Once each layer has been distributed, each 2D slice of the part geometry is fused by selectively melting the powder. This is accomplished with a high-power laser beam, usually an ytterbium fiber laser with hundreds of watts. The laser beam is directed in the X and Y directions with two high frequency scanning mirrors. The laser energy is intense enough to permit full melting (welding) of the particles to form solid metal. The process is repeated layer after layer until the part is complete.
Fused Deposition Modelling

Fused deposition modelling: 1 – nozzle ejecting molten material, 2 – deposited material (modeled part), 3 – controlled movable table | “FDM by Zureks” by Zureks – Own work. Licensed under GFDL via Commons.
FDM begins with a software process which processes an STL file (stereolithography file format), mathematically slicing and orienting the model for the build process. If required, support structures may be generated. The machine may dispense multiple materials to achieve different goals: For example, one may use one material to build up the model and use another as a soluble support structure, or one could use multiple colours of the same type of thermoplastic on the same model.
The model or part is produced by extruding small flattened strings of molten material to form layers as the material hardens immediately after extrusion from the nozzle
A plastic filament or metal wire is unwound from a coil and supplies material to an extrusion nozzle which can turn the flow on and off. There is typically a worm-drive that pushes the filament into the nozzle at a controlled rate.
The nozzle is heated to melt the material. The thermoplastics are heated past their glass transition temperature and are then deposited by an extrusion head.
The nozzle can be moved in both horizontal and vertical directions by a numerically controlled mechanism. The nozzle follows a tool-path controlled by a computer-aided manufacturing (CAM) software package, and the part is built from the bottom up, one layer at a time. Stepper motors or servo motors are typically employed to move the extrusion head. The mechanism used is often an X-Y-Z rectilinear design, although other mechanical designs such as deltabot have been employed.
Selective Laser Sintering
An additive manufacturing layer technology, SLS involves the use of a high power laser (for example, a carbon dioxide laser) to fuse small particles of plastic, metal, ceramic, or glass powders into a mass that has a desired three-dimensional shape. The laser selectively fuses powdered material by scanning cross-sections generated from a 3-D digital description of the part (for example from a CAD file or scan data) on the surface of a powder bed. After each cross-section is scanned, the powder bed is lowered by one layer thickness, a new layer of material is applied on top, and the process is repeated until the part is completed.
Because finished part density depends on peak laser power, rather than laser duration, a SLS machine typically uses a pulsed laser. The SLS machine preheats the bulk powder material in the powder bed somewhat below its melting point, to make it easier for the laser to raise the temperature of the selected regions the rest of the way to the melting point.
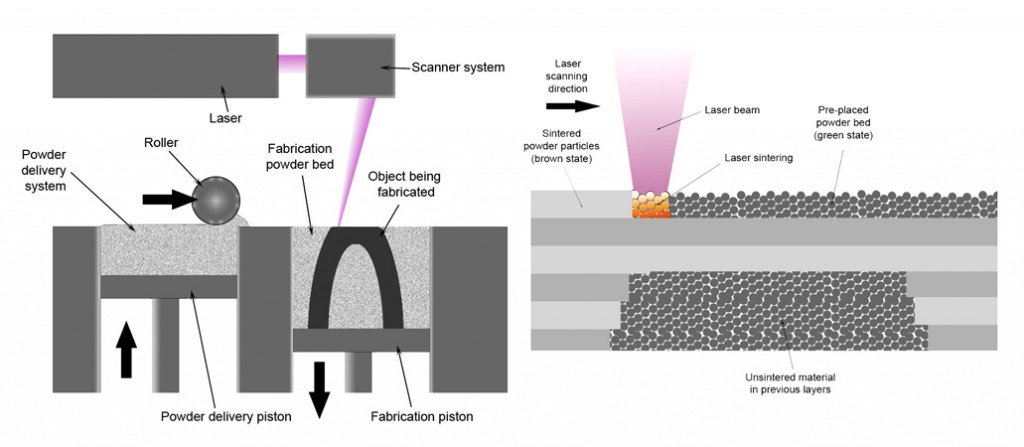
Selective laser sintering process | “Selective laser melting system schematic” by Materialgeeza – Own work. Licensed under CC BY-SA 3.0 via Commons.
Unlike some other additive manufacturing processes, such as stereolithography (SLA) and fused deposition modeling (FDM), SLS does not require support structures because the part being constructed is surrounded by unsintered powder at all times, this allows for the construction of previously impossible geometries.
The Economics of 3D printing
3D printing jobs are an emerging craft in the recent times. A MyCorporation infographic also estimated that it will become a $5.2 billion industry by 2020, with a projected 14 percent annual growth between 2012 and 2017.
As the 3D printing industry booms, what does it mean for job seekers? From designers to nontechnical positions, here are some jobs that will be created or get a boost from 3D printing.
1. 3D design
3D printing relies heavily on designers who can take a product idea and translate it into something that can feasibly be brought to life. Thanks to its growth, 3D printing will create jobs for 3D designers at 3D printing firms, in companies as part of creative teams, and as freelancers.
2. 3D computer aided design (CAD) modeling
3D printing is not be possible without CAD experts, who have the skills and expertise to convert product designs into digital blueprints that 3D printers need. Along with product designers, there is be a demand for 3D CAD modelers. Although 3D CAD professionals are also needed to construct models for mass 3D printing, they are especially important for custom products. As such, 3D CAD modeling jobs will require 3D printing-specific modeling skills, such as feature size, geometrical constraints and knowledge of materials.
3. Research and development
From 3D-printed shoes to 3D-printed clothes and accessories, 3D printing is the fashion of the future. Just as the 3D printing industry will require more product designers and CAD modelers, jobs will also open up for forward-thinking R&D professionals who understand the intersection of tech and consumer products while keeping an eye on the bottom line. Companies will need people who can find the best way to utilize 3D printing for consumer products at the lowest cost possible.
4. Biological and scientific modeling
3D printing is not limited to consumer products. From prosthetics to human tissue, 3D printing promotes medical advancement and saves lives. It can also create drones, defense equipment and maybe even space food. As such, the 3D printing industry will need more engineers, designers and modelers who have a biomedical or scientific background in order to further innovate and produce highly advanced 3D-printed products.
5. Architecture/construction modeling
3D printing will disrupt businesses, particularly those that rely heavily on blueprinting or prototyping. For the construction industry, this paradigm shift will boost the need for 3D modelers that may replace current 2D construction planning solutions. Instead of 2D CAD modeling on paper, 3D printers can produce true-to-life models to better represent what structures will look like.
6. Education
What good are these jobs if no one has the qualifications to fill them? To help fill the skills gap, schools are developing (and some have already launched) 3D printing programs at all grade levels. This will open up jobs for educators who can teach the technical and business aspects of 3D printing.
Teachers will need to have a background in the 3D printing industry. They will also need specific skill sets to teach specialized courses and stay current on the latest trends.
7. Lawyers and legal professionals
3D printing is not confined to the tech world. As a creative field, the 3D printing industry is wide open to legal issues, prompting a need for more lawyers and legal professionals who specialize in intellectual property (IP) rights. As a result, there will be an increased need for IP enforcement actions and lawsuits, as well as expanded services to monitor for infringements, she said.
Growth areas include IP ownership, scope of rights, licensing, fair use, international rights and other forms of IP protection.
8. Business opportunities
Thinking of starting a business? 3D printing offers opportunities for innovation – not only in creating products, but also for entrepreneurship. 3D printing spans all types of technical and design roles, many of which make great business ideas to help others with their 3D printing needs.
With the best 3D printers costing anywhere from $1,999 to $3,500, anyone with 3D printing knowledge can start his or her own 3D printing business, whether on-site, via a website or through an e-commerce marketplace.
9. 3D-Printing-as-a-Service franchises
Not sure if starting from the ground up is for you? 3D printing may be the next hot franchise. According to Forbes.com, UPS recently launched a pilot program testing 3D-Printing-as-a-Service franchises at two of their retail stores in order to make 3D printing mainstream.
One of these UPS stores is located in the San Diego area and is owned by Burke Jones, whose 3D printing waitlist spans three pages of customers ordering robotic arms, custom figurines and vintage parts — just a few examples of the wide range of products offered, according to the Forbes article.
If successful, this and similar 3D-Printing-as-a-Service vendors can bring 3D printing to the masses by providing franchises to local businesses and entrepreneurs. Instead of commissioning a 3D printing company to create products — which is typically done online — 3D-Printing-as-a-Service franchises can provide personalized, in-person 3D printing services to local customers.
10. Operations and administrative positions
3D printing companies don’t run on engineers and technical people alone. As the 3D printing industry grows, new and established 3D printing companies will need people to keep the business running smoothly and on the right trajectory. This includes operations and administrative staff, analysts, finance and sales professionals, and retail employees, among others.
These jobs will open up in all types of 3D printing companies, including vendors, manufacturers and retail stores.
If you are interested in building a career in 3D printing, 3D Printed Jobs is the definite portal for you, where you will get a multitude of 3D Printing Jobs which you can apply for.
Conclusion
3D printing is an interesting topic right now, as it opens up a vast array of possibilities in manufacturing. From artistic designs to medical research to industrial manufacturing, it has revolutionized our lives in myriad ways. Not only that, 3D printing also opens up a vast range of careers one can pursue and it is expected to become an important industry by 2020.